一,Overview
The automotive industry is a typical representative that was the first to form a global industry in modern industry. Automobiles are moving towards lightweight development, demanding fuel savings, increased speed, enhanced durability, comfort and safety. New materials are increasingly being adopted, among which composite materials have become important materials for automobiles.
With increasingly strict environmental regulations worldwide, it objectively prompts automobiles to adopt more and more composite materials. Composite materials are not an independent type of material. With the development of raw materials and improvements in processes, composite materials will be an inevitable trend in the future development of automotive materials.
二,The application of fiberglass reinforced plastic in the automotive industry
Composite materials reinforced with glass fiber (commonly known as "fiberglass reinforced plastic") are one of the important varieties of traditional composite materials. They have been applied in the automotive industry for a long time and have shown a gradually increasing trend in recent years.
China also began to apply fiberglass reinforced plastic (FRP) in automobiles in the 1950s. In the 1980s, Beijing Zhonghua Automobile Company was the first to manufacture FRP bodies. In the 1990s, Zhuhai Gongniu High-Performance Composite Materials Co., Ltd. developed a fully fiberglass reinforced plastic car and put it into mass production in Xi 'an. It also conducted a whole vehicle crash test at Hubei Second Automobile Works, and the anti-collision effect was better than that of the metal body. Wucheng, Shandong Province once manufactured "Qilu" brand all-fiberglass reinforced plastic vans. It is said that there were over 600 related enterprises in Wucheng, Shandong Province alone at that time, which shows the considerable scale. Nowadays, fiberglass reinforced plastic (FRP) is widely used in various types of sedans, buses, trucks and special vehicles in China. Most major automobile manufacturers have established dedicated composite material production workshops or departments, and its application is gradually on the rise.
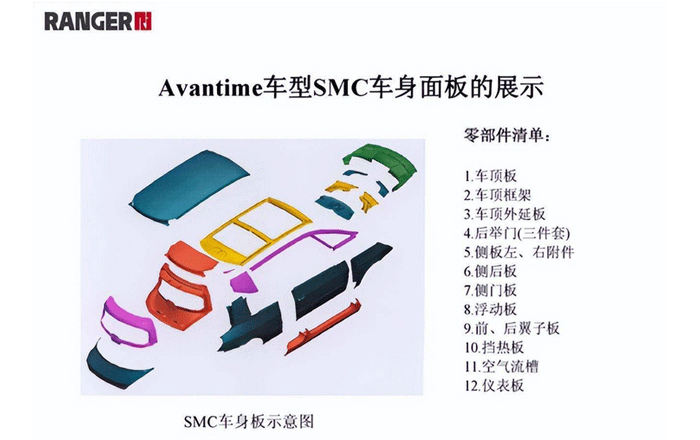
Figure 1 Composite material vehicle body
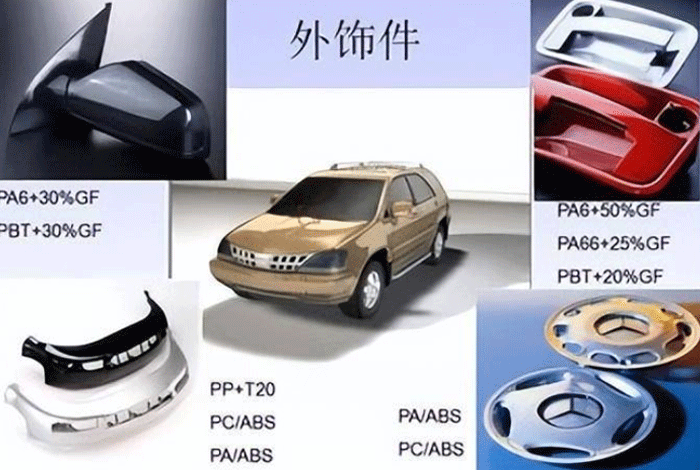
Figure 2 Automotive composite exterior parts
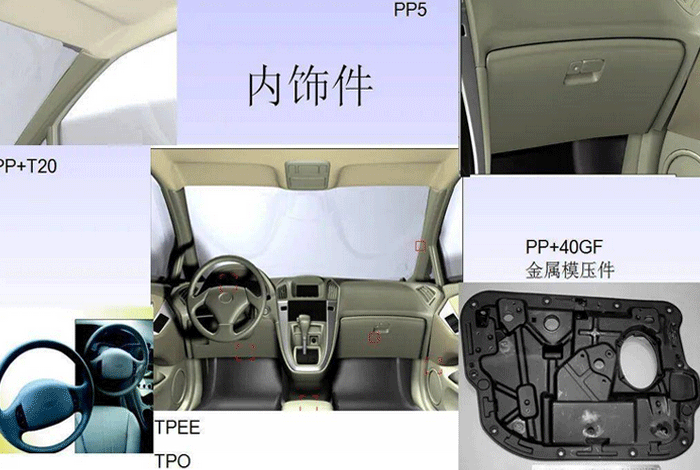
Figure 3 Automotive composite interior parts
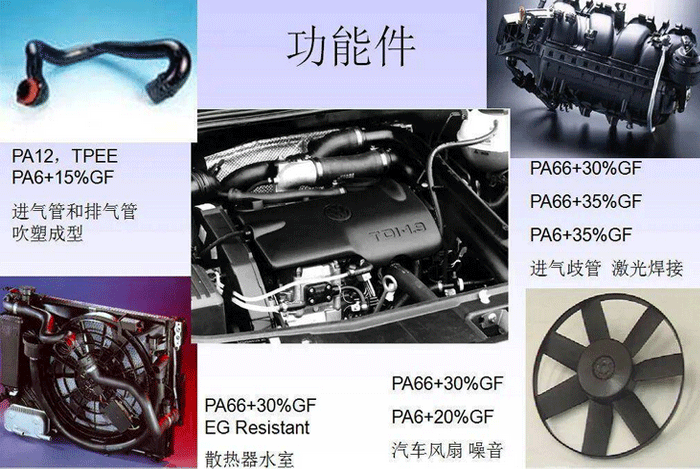
Figure 4 Automotive composite functional parts
FRP/composite material automotive parts are mainly divided into three categories: body parts, structural parts and functional parts.
(1) Body parts: including body shell, roof hardtop, sunroof, doors, radiator grille, headlight reflector, front and rear bumpers, and interior parts, etc. These are mainly to meet the needs of streamlined body design and high-quality appearance. This is the main direction of fiberglass reinforced plastic (FRP) application in automobiles. Currently, the development and application potential is still huge. Typical forming processes include: SMC/BMC, RTM and hand lay-up/jet, etc.
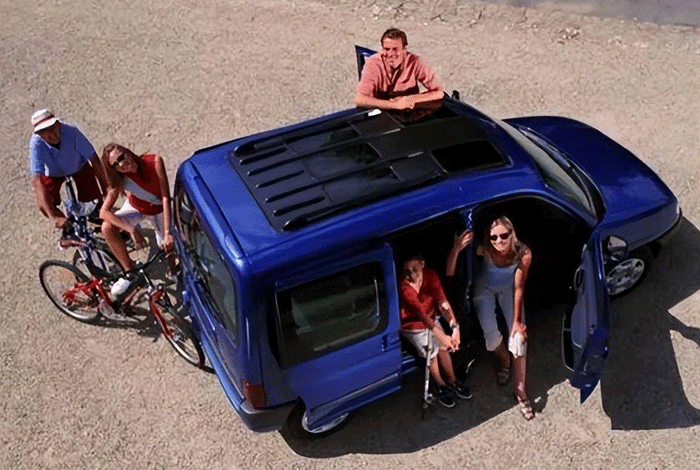
Figure 5 shows the SMC multi-functional roof of the Citroen berlinggo model
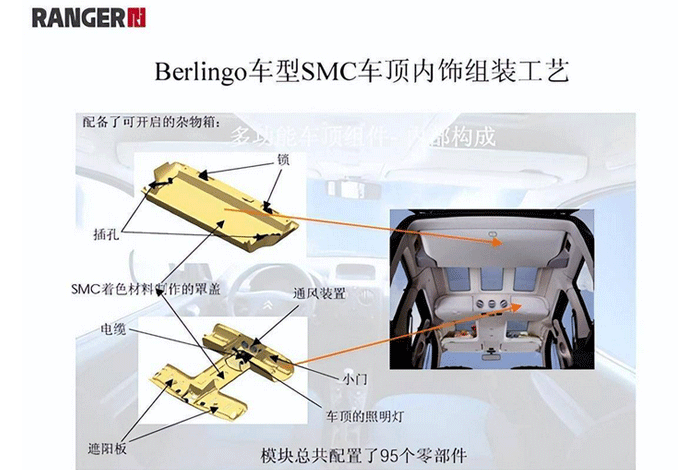
Figure 6 shows the assembly process of the SMC roof interior of the berlinggo model
(2) Structural components: including front-end brackets, bumper frames, seat frames, floors, etc., the purpose of which is to enhance the design freedom, multi-functionality and integrity of the components. The main materials used are high-strength SMC, GMT, LFT, etc.
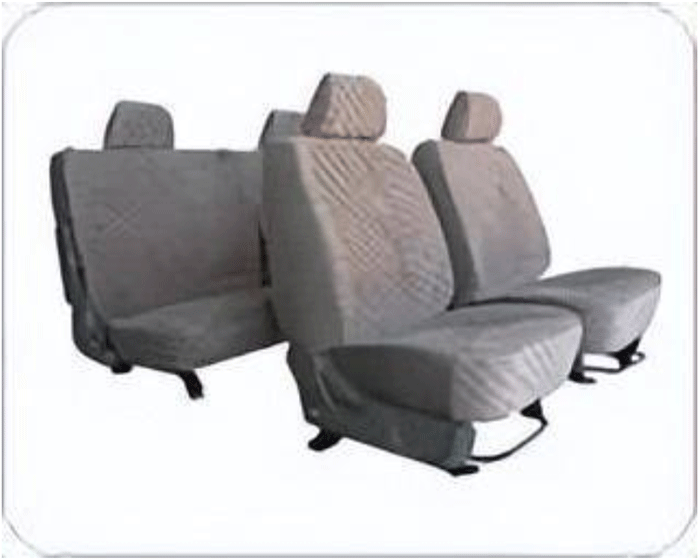
Figure 7 Seat bracket
(3) Functional components: They are required to be resistant to high temperatures, oil corrosion, etc., mainly focusing on engines and peripheral parts. Such as: engine valve cover, intake manifold, oil pan, air filter cover, gear compartment cover, air deflector, intake pipe guard plate, fan blade, fan air deflector ring, heater cover plate, radiator component, water outlet shell, water pump turbine, engine sound insulation board, etc. The main process materials are: SMC/BMC, RTM, GMT and glass fiber reinforced nylon, etc.
Figure 8 Material composition of intake manifolds for different vehicle models
Figure 9 Intake manifold
Figure 10 Radiator water chamber
(4) Other related components: such as CNG gas cylinders, components for sanitary facilities of passenger vehicles and recreational vehicles, motorcycle components, anti-glare panels and anti-collision posts on expressways, highway isolation posts, and roof cabinets for commodity inspection vehicles, etc.
Figure 11 CNG gas cylinders for vehicles
The United States is the world's largest producer and consumer of fiberglass reinforced plastic (FRP)/composite materials. The extensive use of FRP in automobiles in the United States has achieved remarkable results in automotive lightweighting. It is estimated that the current annual consumption of composite materials for automobiles in the United States exceeds 700,000 tons. Among them, 32% of the thermosetting composites are used in the automotive and related fields, and a considerable number of components adopt the SMC molding process. In the United States, 65% of American cars use SMC for the front face and radiator grille. More than 95% of automotive headlamp reflectors have adopted BMC as the main material. The application of composite materials in automobiles almost covers all domestic automobile manufacturers in the United States, such as the three major automobile companies, General Motors, Ford, and DaimlerChrysler (DC), as well as heavy vehicle manufacturers like Mack and Aero-star.